Comparing FDM vs. SLA vs. SLS: 3D Printing Technology.
- S B Arjun Dhilip
- Jan 19
- 4 min read
FDM vs Other 3D Technologies: A Comprehensive Comparison
In the world of 3D printing, choosing the right technology is crucial to achieving your desired results efficiently and cost-effectively. Among the many 3D printing types, FDM (Fused Deposition Modeling), SLA (Stereolithography), and SLS (Selective Laser Sintering) are three of the most popular technologies. Each has its strengths, limitations, and ideal use cases. This blog dives deep into the differences between these technologies, highlighting their pros and cons, and provides guidance on selecting the best one for your needs.
Summary
What Is FDM 3D Printing?

FDM 3D printing is the most widely recognized technology in additive manufacturing. It works by extruding thermoplastic filaments layer by layer to build an object. FDM printers are known for their affordability and ease of use, making them ideal for hobbyists and beginners.
Pros of FDM
Cost-effective: The low cost of FDM printers and filaments makes them highly accessible.
Ease of use: Suitable for individuals with minimal technical expertise.
Material variety: Filaments like PLA, ABS, and PETG offer flexibility for various projects.
Cons of FDM
Lower precision: Compared to SLA and SLS, FDM struggles with fine details.
Surface finish: Often requires post-processing for a smooth appearance.
Strength limitations: Parts may lack isotropy, making them weaker in certain directions.
Use Cases: Prototyping, educational models, and simple functional parts.
What Is SLA 3D Printing?
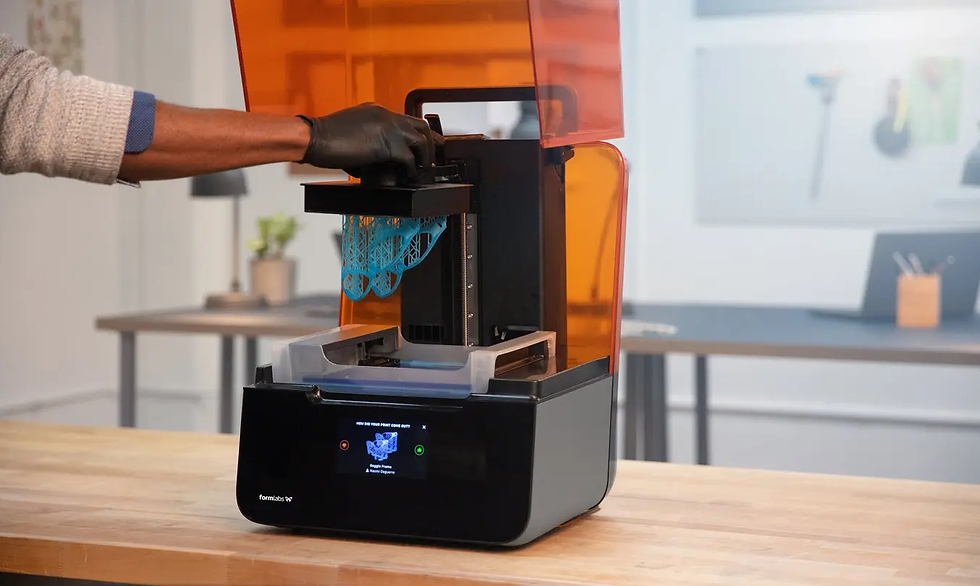
SLA 3D printing uses a UV laser to cure liquid resin into solid layers, resulting in highly detailed and smooth objects. SLA is renowned for its precision, making it the go-to technology for industries requiring intricate designs.
Pros of SLA
Unmatched precision: Ideal for detailed parts and fine geometries.
Smooth surface finish: Requires minimal post-processing for aesthetics.
Versatility in applications: Suitable for dental models, jewelry, and artistic creations.
Cons of SLA
Higher cost: Resin and printer maintenance can be expensive.
Complex workflow: Resin handling and post-curing require more expertise.
Limited durability: SLA parts may be less robust than those produced by SLS.
Use Cases: Medical devices, detailed prototypes, and aesthetic models.
What Is SLS 3D Printing?

SLS 3D printing uses a laser to fuse powdered material, layer by layer, into a solid object. SLS is known for producing durable, functional parts with complex geometries.
Pros of SLS
Durability: Creates robust parts suitable for end-use applications.
Complex designs: Handles intricate geometries without support structures.
Isotropic properties: Parts have consistent strength in all directions.
Cons of SLS
High cost: Equipment and materials are expensive, making SLS less accessible to beginners.
Rough surface finish: Parts often require post-processing for smoother aesthetics.
Limited accessibility: Requires professional expertise for optimal operation.
Use Cases: Aerospace components, automotive parts, and industrial-grade prototypes.
FDM vs SLA vs SLS: Compare Filament, Resin, and Powder 3D Printers

Understanding the differences between these technologies is key to making an informed decision. Let’s break down their performance across key parameters.
Category | FDM | SLA | SLS |
---|---|---|---|
Precision and Resolution | Moderate resolution, struggles with fine details. | Excels in precision with smooth, detailed parts for small-scale projects. | Balances precision with durability, highly accurate functional parts. |
Dimensional Accuracy and Precision | Slight inaccuracies due to material warping, especially in larger parts. | Unparalleled accuracy for applications requiring high precision. | Consistent dimensional accuracy, even in complex designs. |
Surface Finish | Visible layer lines, requires sanding or coating for smooth finish. | Polished surfaces straight from the printer. | Rough surfaces, can be smoothed through post-processing. |
Workflow and Ease of Use | Beginner-friendly, minimal setup, straightforward operation. | More involved workflow with resin handling and curing | Complex workflow, suited for experienced users and industrial setups. |
Materials and Applications | Wide range of affordable filaments like PLA, ABS, and PETG. | Specialized resins for precision-driven applications. | Durable powders like nylon for functional, load-bearing parts. |
Build Volume | Supports large-scale projects at a low cost. | Limited to smaller builds due to resin constraints. | Medium to large build volumes for industrial applications. |
Speed and Throughput | Relatively fast for simple designs, slower for complex models. | Moderate speed, with curing time adding to the process. | High throughput, especially suitable for batch production. |
Costs and ROI | Most affordable, quick ROI for prototyping. | Higher initial costs, justified for precision applications. | Expensive setup, suitable for high-volume, industrial needs. |
Using FDM, SLA, and SLS 3D Printers Together
For businesses with diverse requirements, combining these technologies can maximize efficiency and output quality. For example:
Use FDM for initial prototypes to test fit and functionality.
Use SLA for detailed models requiring high precision and aesthetic appeal.
Use SLS for producing durable, end-use components or small-batch manufacturing.
This hybrid approach leverages the strengths of each technology, ensuring cost-effective and high-quality production.
Key Takeaways
FDM
Best for cost-effective prototyping and hobbyist projects.
Prioritizes affordability over precision.
SLA
Ideal for industries needing detailed, smooth, and precise parts.
Involves higher costs and a complex workflow.
SLS
Perfect for durable, functional parts in industrial settings.
Offers high throughput but comes with significant upfront investment.
When deciding between FDM vs other 3D technologies, consider factors like precision, cost, speed, and use cases. Whether you’re a beginner exploring 3D printing types or a professional seeking advanced manufacturing solutions, there’s a technology tailored to your needs.
Want personalized guidance on choosing the best FDM printer or tips for mastering 3D printing ? Contact us for a free consultation today!
Comments